Important note
The purpose of this Guideline is to assist the owners of small tugs of not more than 15 gross tonnage to complete their Small Vessel Detailed Compliance Report (Form 85-0525E). Each guidance note is associated with a question on the Small Vessel Detailed Compliance Report, a copy of which can be found at the SVCP Enrollment Page.
The Small Vessel Detailed Compliance Report and these Guidelines do not replace the regulations and the final authority for any regulatory requirement is the latest relevant regulations. References to regulations and standards are included in this document; however, this list is not exhaustive of all relevant regulations and standards. The reader should consult the Department of Justice website for a comprehensive list of the latest regulations under the Canada Shipping Act, 2001.
On this page
- Vessel information
- Section 1: Vessel registration and operations
- Section 2: Construction, stability and watertightness
- Section 3: Navigational safety and equipment
- Section 4: Vessel manning and crew qualifications
- Section 5: Pollution prevention
- Section 6: Electrical systems/batteries
- Section 7: Fuel systems
- Section 8: Machinery
- Section 9: Life saving and fire safety equipment
Vessel information
Gross tonnage (GT)
Gross tonnage is the measure of the overall size of a vessel as determined in accordance with the Vessel Registration and Tonnage Regulations and the Standard for the Tonnage Measurement of Ships (TP 13430) (available at https://tc.canada.ca/en/marine-transportation/marine-safety/marine-safety-publications), by using one of the following:
- Form 4A: Simplified Method of Tonnage Measurement;
- Form 4B: Tonnage Measurement of a Simple Multihull Vessel; or
- A duly appointed Tonnage Measurer.
The forms and additional information are available at https://tc.canada.ca/en/marine-transportation/vessel-licensing-registration.
Year built
If you do not know the year that your vessel was built, indicate “1900” as the year built on page 1.
Area of operation
Sheltered waters, voyage means a voyage that is
- in Canada on a river above tidal waters or on a lake, where it is impossible for a vessel to be more than 2.5 nautical miles from the closest shore;
- on the waters listed in column 1 of Schedule 1 during the period specified in column 2; or
- made by a ferry between two or more points listed in column 1 of Schedule 2 during the period specified in column 2.
Inland Voyage, means a voyage that is not a sheltered waters voyage and is
- on the inland waters of Canada; or
- on the inland waters of Canada together with any part of a lake or river forming part of the inland waters of Canada that lies within the United States, or on Lake Michigan.
Near coastal voyage, Class 2, means a voyage
- that is not a sheltered waters voyage or an inland voyage; and
- during which a vessel is always
- 25 nautical miles or less from shore in waters contiguous to Canada, the United States (except Hawaii) or Saint Pierre and Miquelon, and
- 100 nautical miles or less from a place of refuge.
Near coastal voyage, Class 1, means a voyage
- that is not a sheltered waters voyage, an inland voyage or a near coastal voyage, Class 2;
- that is between places in Canada, the United States (except Hawaii), Saint Pierre and Miquelon, the West Indies, Mexico, or Central America, or on the northeast coast of South America, including on any navigable waters connected with that coast; and
- during which a vessel is always
- north of latitude 6°N, and
- 200 nautical miles or less from shore or above the continental shelf.
Unlimited Voyage, means a voyage that is not a sheltered waters voyage, an inland voyage, a near coastal voyage, Class 2 or a near coastal voyage, Class 1.
Note: The definitions of the voyage classifications are found in the Vessel Safety Certificate Regulations, section 1.
Principal operator certification and training
Master Limited. The general requirements for Master Limited can be found in section 131 of the Marine Personnel Regulations. The Master Limited training program description is found in Chapter 12 of Transport Publication (TP) 2293 available at https://tc.canada.ca/en/publications/marine-publications-abstracts .
ROCM - Restricted Operator’s Certificate (Maritime). The ROC(M) is required by anyone using a marine VHF radio or other marine radios (each person on the boat who will use the radio needs their own card).
ROCMC – Restricted Operator’s Certificate – Maritime Commercial. The Restricted Operator‘s Certificate - Maritime Commercial (ROC-MC) is intended for mariners serving on compulsorily-fitted non-pleasure vessels within the North American A1 Sea Area as defined in Radio Aids to Marine Navigation (available through the Canadian Coast Guard at www.ccg-gcc.gc.ca).
First Aid – “Marine advance first aid certificate” is required by any person designated to provide first aid on board a vessel that is engaged on a near coastal voyage, class 1 or unlimited voyage. “Marine basic first aid certificate” is required by any person designated to provide first aid on board a vessel that is engaged on a near coastal voyage, class 2, Inland voyage or sheltered waters voyage.
MED A3 – Marine Emergency Duties A3 (Small Non-Pleasure Vessel Basic Safety). The MED A3 training program description is found in Transport Publication (TP) 4957 available at https://tc.canada.ca/en/publications/marine-publications-abstracts .
SVMO – Small Vessel Machinery Operator. The general requirements for SVMO can be found in section 151 of the Marine Personnel Regulations. The SVMO training program description is found in Chapter 33 of Transport Publication (TP) 2293 available at https://tc.canada.ca/en/publications/marine-publications-abstracts.
Additional resource are available at:
- https://tc.canada.ca/en/marine-transportation/marine-safety/personnel-training-examination-certification
- Register to the YouTube channel of the Transportation Safety Board (TSB)
- Transport Canada Small Commercial Vessel Safety Guide - TP 14070 E (2010) (PDF, 8.3 MB) (Stay tune for the new version that will be release in 2022, which will be available on via https://tc.canada.ca/en/marine-transportation/marine-safety
- Other guide, not made for the towing industry specifically but complete with best practice and free tools for every mariner:
- For the free Safety Checklists, Marine Quick Reference Guide, Safety for all vessels and Crew, see: Gearing up for safety from WorkSafe BC.
- Working Safety on the Fraser River, Best practices for all vessels is another great product from WorkSafe BC
- For guidance on how to develop a safety management system and How to familiarize new people on board: Comité permanent sur la sécurité des bateaux de pêche du Québec (CPSBPQ)
Section 1: Vessel registration and operations
General statement
The following general statement is to be taken into account for questions number 5 to 18:
The authorized representative must ensure that the vessel, its machinery and equipment meet the requirements of the regulations, develop procedures for the safe operation of the vessel and for dealing with emergencies, and ensure that the crew and passengers receive safety training.
The responsibilities of a vessel’s authorized representative, master and crew concerning vessel safety are set out in Part 4 of the Canada Shipping Act, 2001.
Note: For more information on developing procedures, and to find templates for procedures common to normal operation of most vessels, visit https://tc.canada.ca/en/marine-transportation/marine-safety/templates-small-commercial-vessel-procedures-records. Your tug will require additional safe operating procedure, has highlighted in various section of this guidelines.
Question 1 (Is the vessel registered?)
Section 46 of the Canada Shipping Act, 2001 (CSA 2001) requires that all vessels (except for those listed below) be registered in either the Canadian Register of Vessels or in the Small Vessel Register. No vessel shall be operated without a valid Certificate of Registry if that vessel is required to be registered.
You are not required to register vessels that carry less than 12 passengers, and if it is a:
- Commercial human-powered vessel, such as canoes and kayaks, or
- Small sailing vessel less than 8.5 meters, or
- Small power-driven vessel with motors less than 7.5 kW (10 horsepower).
If your small commercial vessel is exempt, you can still choose to register it voluntarily.
You can find a full list of exemptions in the Vessel Registration and Tonnage Regulations, Subsection 1.1. If you own and operate an exempt vessel, you must still comply with all construction , safety and pollution prevention requirements.
All information, including payment, is available online via the new Transport Canada website : Apply for or manage a vessel registration
Vessel Registration Forms webpage.
Need help? For general questions or if you can't submit or pay your application online, call:
- Toll-free telephone: 1-877-242-8770
- TTY: 1-888-675-6863
Hours of operation are Monday to Friday, 8:00 a.m. to 5:00 p.m. EST
For technical support or for specific questions, email vr-ib@tc.gc.ca.
Important fact!
A valid certificate of registry must be on board your vessel at all times.
If any information in your certificate of registry changes, you must report the change within 30 days. A new certificate of registry for every vessel affected by the change will be re-issued for free.
You must report changes to:
- your personal information
- the authorized representatives information
- the vessel details
If a change isn't reported, your vessel's registration may be suspended or cancelled.
Operating an unregistered vessel could result in a fine. The penalty for operating an unregistered vessel is $260 to $10,000 per day.
(Canada Shipping Act, 2001, Section 46), (Vessel Registration and Tonnage Regulations, Subsection 1.1)
Question 2 (Is the official number, name and port of registry (if applicable) marked on the vessel as per the vessel registrar?)
Your Certificate of Registry is not valid until the vessel has been marked in accordance with the instructions on the Certificate of Registry.
If your vessel is registered in the Small Vessel Register, it must be marked with the Official Number (C Number, example: C12345AB) in block characters not less than 75 millimetres high and in a colour that is in contrast with the background. This Registration number must be located on each side of the bow of the vessel, or on a board permanently attached to the vessel as close to the bow as practicable.
If your vessel is registered in the Canadian Register of Vessels, it must be marked with the name of the vessel and Port of Registry in clearly legible letters (Latin alphabet or Arabic or Roman numerals) at least 10 centimetres in height, on some clearly visible exterior part of the hull such as the bow and the stern. The Official Number (example: O.N. 897654) and registered tonnage must be marked on some clearly visible interior part of the hull in block-type Arabic numerals at least 4 centimetres in height.
More info via Marking your vessel website.
(Canada Shipping Act 2001, Section 57)
Question 3 (Is a copy of the certificate of registry on board?)
Once a Certificate of Registry has been issued, a copy of it must be carried on board at all times. No person shall operate a vessel in respect of which a certificate of registry or provisional certificate has been issued unless the certificate is on board.
(Canada Shipping Act 2001, Section 63)
Question 4 (Since it was built, have any structural/mechanical changes occurred to the vessel?)
To ensure that your certificate remains valid, any change(s) to the information shown on the Certificate, including a change of address, must be reported to the vessel registry within 30 days of the change: vr-ib@tc.gc.ca
(Canada Shipping Act 2001, Section 58)
Question 5 (Have you ensured the crew has a firm understanding of the stability book's contents?)
It is the responsibility of the vessel’s crew to carry out their duties and functions in a manner that does not jeopardize the safety of the vessel or of any person on board and to report to the master any safety hazards of which they become aware or any change in circumstances that could affect their ability to carry out their duties and functions safely. To do this effectively, the crew must be aware of the stability characteristics of the vessel and what conditions may negatively affect that stability in order to identify when changing conditions may present a hazard to safety.
Crew training materials should include explanation of any information contained in the vessel’s stability book identifying the stability limitations for the loading and operation of the tug.
If your response to this question is ‘No’, operating procedures, training materials, a stability notice etc. should be developed as necessary to ensure the crew firmly understands the contents of the vessel’s stability book.
(Canada Shipping Act 2001, Section 106)
Question 6 (Does the crew have a firm understanding of the tug's operational limitations before any operation?)
As the Authorized Representative, has clear guidance been provided to the crew as to the operational limitations of the tug? This may include size of the tow, weather limits, and geographical locations, i.e. fast currents, large tides, how and where dangerous local conditions that can develop etc.?
Good operating practice should include a review and crew briefing of factors that may present hazards to safety prior to the commencing of an operation. This should include the inherent risks due to stability and vessel limitations referred to in Question 5 and also changing operational factors such as the size of the tow, weather conditions, fast currents, large tides and other local navigational hazards.
If your response to this question is ‘No’, operating procedures and/or training materials should be developed as necessary to ensure the crew firmly understands the tug’s operational limitations prior to any operation.
Other guidance:
- “Recommendations to be applied to every tug which is employed in towing Vessels on a long line astern”
- See TSB Tugboat Capsizes Off B.C. Coast YouTube Video
(Canada Shipping Act 2001, Section 106)
Question 7 (Are there procedures in place for assessing the tug's suitability to safely carry out its intended operations?)
How is it determined that the tug is suitable for the intended operation? Is the tow and its characteristics considered when determining suitability? Are all of the various factors taken into consideration when assigning duties to the tug and its crew?
The ability of the master and crew to meet those responsibilities begins with an accurate assessment of a tug’s capabilities and suitability to safely carry out an intended operation, especially for new operating with potentially unknown risks. This assessment should include an evaluation of the tug’s performance characteristics and power available to control a tow or perform other required operations and various other factors that may affect suitability including a consideration of a crew’s ability to perform required work to complete the operating given the number of crew members, their qualifications, hours of work/rest requirements etc.
If your response to this question is ‘No’, operating procedures and/or training materials must be developed as necessary to the suitability of the tug is assessed to safely carry out its intended operations.
Other guidance:
- See SSB No.: 16/2020 - Hazards and Risks of Girding During Towing Operations for information about girding
(Small Vessel Regulations, Section 521)
Question 8 (Is there a procedure to assess the tugs bollard pull and is it suitable for its intended operations?)
The bollard pull of a tug can be measured to determine the maximum pulling force the propulsion engines can develop. Knowing this bollard pull value is important when assessing the tug’s ability to handle certain sized tows when all of the environmental conditions are accounted for. In addition, specialists can determine the outcome if the tug is matched to its tow under the anticipated conditions.
A tug’s bollard pull is vital to know to assess its suitability to safely carry out intended operations and for the crew to understand its operational limitations and should be readily available to the master and crew. If you answered ‘No’ to this question, the bollard pull of the tug should be measured and added to the operating procedures and/or training material as needed.
In the absence of more specific information, the following empirical formula is widely used for determining the estimated bollard pull required for any type of tow:
Where:
- BP = required bollard pull (tons)
- Δ = full displacement of towed vessel (tons)
- V = tow speed (knots)
- B = breadth of towed vessel (metres)
- D1 = depth of the exposed transverse section of the towed vessel including deck cargo, measured above the waterline (metres)
- K = a factor that reflects potential weather and sea conditions
- For exposed coastal tows; K = 1.5 to 2.0
- For sheltered coastal tows; K = 0.5 to 1.5
- For protected water tows; K = 0.5
Other guidance:
- TP11960 “Appendix “A” - Guidance for Tug and Barge Towing Systems”
- Section 1.3 Bollard Pull of Towing Vessel
- Bollard Pull test: https://www.youtube.com/watch?v=GIhbRsHO2v0
- Bollard Pull Test Procedure: https://www.youtube.com/watch?v=_92PG_J6EAs
(Canada Shipping Act 2001, Section 106)
Question 9 (Is the towing equipment installation compliant with the regulations?)
Answer ‘Yes’ to this question if the towing equipment installation meets all of the following requirements:
- At the control position of a towing winch, there must be a means of two-way communication with each steering position that is not in direct voice contact;
- Each steering position must have a control to immediately reduce tension on a towline connected to a winch. On an existing ship without such control, the winch must have an effective winch drum brake that can be applied and released by hand without the use of a bar and a mechanism to effectively secure any clutch that transmits power to the winch drum in the disengaged position;
- Where a winch can be controlled from more than one position, there must be arrangements to prevent more than one control position to operate at any one time, and every winch control must be fitted with a safe guard to prevent its inadvertent operation;
- A ratchet device that could prevent the winch from paying out the towline must not be fitted on a towing winch;
- Where a towline is attached to a bollard or to bitts, the vessel must be equipped with a mechanical arrangement able to immediately sever or release the towline or an axe to cut the towlines that is clearly marked to indicate its purpose and stowed near to bollard or bitts;
- Where a towline is attached to a hook, each steering position must have a control able to immediately release the towline from the hook;
- A tug with more than 373 kW brake power, must have power operated towing pins if they are fitted with their control position forward of the point of tow. The pins must be clearly visible from the control position.
If your tug is more than 5 GT, unless it is used only for salvaging logs, sections 131 to 138 of Part VIII of the Hull Construction Regulations apply for any towing equipment that is fitted.
Other guidance:
- Tugs and Tows – A Practical Safety and Operational Guide (PDF, 3.02 MB)
(Hull Construction Regulations, Part VIII Section 131-138)
Question 10 (Are there procedures in place for maintaining the emergency towline abort (release) system?)
The emergency towline abort (release) system is a critical safety feature that must be maintained to ensure it operate properly when needed in an emergency.
If you answered ‘No’ to this question, procedures for maintaining the emergency towline abort (release) system should be added to the tug’s operating procedures and training materials. If the condition or operation of the system is unknown, it should be maintained and/or tested prior to under towing.
Other guidance:
- Emergency towing quick release video: https://youtu.be/BQvUCLJAJoY
(Canada Shipping Act 2001, Section 106)
Question 11 (Is the emergency abort (release) system tested at all conning stations before undertaking the tow?)
Prior to starting a towing operation, it should be standard operating practice to test the emergency abort (release) system locally at the winch control and at all steering positions/stations. When the system is activated does the winch clutch release as well as the brake? Is the tow winch drum free to rotate when the system is aborted?
If you answered ‘No’ to this question, procedures for testing the emergency towline abort (release) system prior to starting a towing operation should be added to the tug’s operating procedures and training materials.
(Hull Construction Regulations, Part VIII Section 135), (Small Vessel Regulations, Section 521)
Question 12 (Do you or the master provide a pre-departure checklist for the crew to carry out?)
The inclusion of a pre-departure checklist is an important tool of good operating practice to include as part of a vessel’s standard operating procedures that a crew can use to identify potential problems before they are able to develop into greater hazards. A pre-departure checklist is an effective means to ensure that critical operational procedures aren’t overlooked or forgotten.
If you answered ‘No’ to this question, consider adding a pre-departure checklist to your tug’s operating procedures.
(Canada Shipping Act 2001, Section 106)
Question 13 (Does the crew have specific training or the experience necessary to safely carry out the intended operations?)
Towing is a specialized skill that requires experience to obtain, does the crew have the necessary experience to safely undertake the intended voyage?
The Canada Shipping Act, 2001, subsection 106(1), requires the authorized representative (AR) of all towing vessels to create safety and emergency procedures and to ensure that the crew receive safety training. These should include best practices from industry.
The Marine Personnel Regulations, subsection 206(2), requires that the master of a vessel shall ensure that the vessel’s crew is trained on their assigned duties (e.g. towing equipment and how to use it safely, during both normal operations and in an emergency).
(Canada Shipping Act 2001, Section 106)
Question 14 (Is there a tow plan in place before every operation to ensure safety of the vessel and crew?)
The responsibilities of a vessel’s authorized representative, master and crew concerning vessel safety are set out in Part 4 of the Canada Shipping Act, 2001.
Planning before undertaking a towing operation is a critical step in avoiding the occurrence of unanticipated incidents, even for routine operations to minimize the unexpected and avoid hazards.
Consider including the following in the tow plan:
- Completion of procedures to assess the tug's suitability to safely carry out the intended operation, including the adequacy of its available horse power, bollard pull and manning etc. for the vessel to be towed;
- Completion of procedures to ensure the crew’s knowledge of the tug’s stability and operational limitations;
- Completion of a pre-departure checklist;
- Knowledge of Stability information and other particulars/limitations of the tow;
- Procedures for the inspection of the tow prior to the operation;
- The equipment needs for the tow with operating procedures;
- Pre-testing emergency systems/aborts of towing winches;
- Procedures for connecting and disconnecting from the tow;
- A review of the Notice to Mariners relative to the voyage route and a list of all navigation hazards, restrictions, bridges etc. that are expected during the voyage;
- Weather forecasts;
- A list of contact information for shore and tow personnel, emergency services etc.;
- A list of provisions/consumables needed for the tow.
(Canada Shipping Act 2001, Section 106)
Question 15 (Does the crew have specific knowledge/training of the cause and effect of girding while towing?)
As the owner of the tug, have you trained Masters and crew on the cause and effects of girding the tug? Do geographic locations during the tug’s voyage make girding of the tug a higher possibility, i.e. currents, weather forecasts etc?
Other guidance:
- See “SSB No.: 16/2020 – “Hazards and Risks of Girding During Towing Operations” for more information about girding
- TSB Girding Video: Tug Girding - YouTube
Question 16 (Are procedures in place to help prevent girding when towing?)
What provisions has the AR taken to ensure that the crew is adequately educated to minimize the effects of a girding situation? Does the company have procedures in place restricting vessel operation during high risk girding situations, i.e. tide and current etc.?
Other guidance:
- See “SSB No.: 16/2020 – “Hazards and Risks of Girding During Towing Operations” for more information about girding
- TSB Girding Video: Tug Girding - YouTube
Question 17 (Is aft of the towline clear of obstructions to allow it to swing freely?)
This question addresses Paragraph 521(d) of Small Vessel Regulations and is to remind operators of small workboats that may infrequently engage in towing operations that there should be no obstructions aft of the attachment point of the towline on the tug that could interfere with the swing of the towline.
Other guidance:
(Small Vessel Regulations, Section 521)
Question 18 (Is the towing gear maintained in accordance with industry best practices?)
Vessels over 5 gross tons that were built or converted for towing must follow Part VIII of the Hull Construction Regulations
Other guidance:
- TP11960 “Appendix “A” - Guidance for Tug and Barge Towing Systems”
- “Ship owners’ Club: Tug and Tow – A Practical Safety and Operational Guide”
- SSB No.: 16/2020 - “Hazards and Risks of Girding During Towing Operations”
(Canada Shipping Act 2001, Section 106), (Hull Construction Regulations, Part VIII)
Question 19 (Are there emergency procedures in place?)
Emergencies happen when least expected. Practicing responses to a variety of emergency situations will enable crewmembers to react quickly and properly to any situation. Consider scenarios applicable to your area of operation. Procedures should be established for the use of the life-saving appliances and fire extinguishing equipment in case of an emergency; and the crew practices the procedures so as to be at all times proficient in carrying them out.
(Small Vessel Regulations, Section 520)
Section 2: Construction, stability and watertightness
Question 20 (Are watertight bulkheads located in the required locations and fitted with watertight closing appliances?)
Answer ‘Yes’ to this question if the location of any fitted watertight bulkheads and the means of closing any opening within those bulkheads meet the requirements below.
If your tug is more than 5 GT, unless it is used only for salvaging logs,
- sections 109 of Part VIII of the Hull Construction Regulations requires a collision bulkhead be fitted in an approved location and watertight bulkheads fitted at the forward and aft end of the engine room (placed as close together as is practicable);
- if the tug is a new tug, sections 110 and 111 require openings, other than tank manholes, in these bulkheads to be
- an approved watertight closing appliance;
- in combination with the reinforcing of the opening, at least as strong as the unpierced bulkhead;
- capable of being opened and closed watertight from each side of the bulkhead; and
- provided with a position indicator light in the wheelhouse that is
- actuated by the closing appliance,
- lighted when the closing appliance is open,
- serviced by a standby circuit and lamp that are automatically brought into operation when the normal circuit or lamp fails, and
- visible by the helmsman at the main steering position.
If the tug’s gross tonnage is five or less, or it is used only for salvaging logs, or it is considered an existing2 ship (i.e. not a new ship as defined above), you may enter ‘N/A’ for this question.
Closing appliances in watertight Bulkheads (HCR s.110) are also noted in Question 24.
(Hull Construction Regulations, Part VIII Section 109-111)
Question 21 (Has the vessel had a stability assessment?
In addition to the conditions encountered by all vessels in a seaway, tugs are subject to external forces created by the towline.
If not properly managed these forces could result in rapid capsize of the vessel.
- See TSB Tugboat Capsizes Off B.C. Coast YouTube Video
The best way to prevent a boat from capsizing is to operate a well-designed, maintained and loaded vessel with an experienced crew.
Preventing unstable vessel conditions and being able to recognize the warning signs when such conditions do occur can save lives.
Having a stability assessment made, in combination with appropriate operating procedures, is the best way to ensure that the stability remain adequate. Some guidance on stability is provided below.
Guidance on stability while towing
The towline force has to be counteracted by the tug and this is done by the thruster forces or by the drag forces or by a combination of both.
A thruster force in the direction of the towline is needed for horizontal equilibrium. In the case of a tug with an aft towing point, a thruster force in the opposite direction of the towline is needed.
In the above image, the transverse stability moment consists of two forces in opposite direction: the downward vertical acting weight force and the upward vertical acting buoyancy force. The lever of this moment is called the stability lever.
With the towline force, two other forces are acting on the tug, the drag force and the thruster forces. The thruster forces can act in the same direction as the towline, counteracting the heeling moment, or in the opposite direction, thereby increasing the heeling moment.
The towline force and the drag and thruster forces cause a heeling moment which has to be counteracted by the transverse stability moment of the tug.
Precautions
Of all accident types, founders and capsizes caused by a loss of stability are the most likely to lead to death on the water. It is possible to avoid many of these accidents. A well-designed vessel will resist capsizing or foundering in severe conditions if it is operated properly. Keep these rules in mind:
- Do not perform towing operations unless the stability of your vessel has been assessed under these conditions;
- Adjust course, speed, or both if you can, to reduce the vessel’s rolling motion;
- Avoid sharp turns or turns at high speed;
- Consult a marine professional before making changes, because modifications to your vessel may affect its stability. Have the stability information revised to reflect any changes you make to the vessel.
Warning signs of instability
- Your vessel’s handling changes. For example, it seems sluggish, rolls more or rolls more slowly;
- Your vessel is listing to one side or is trimmed more than usual by the bow or stern;
- There is less freeboard than you would expect normally. If so, check tanks and holds for flooding or cargo shift;
- The bilge pumps are working more frequently than usual. If this happens, check the bilge for water, and if bilge pumps and alarms are working properly.
Section 601(2) of the Small Vessel Regulations requires the owner and the operator of a vessel other than a pleasure craft to ensure the vessel has adequate stability and structural strength to safely carry out its intended operations.
If your tug is more than 5 gross tonnage, Sections 104 to 108 of Part VIII of the Hull Construction Regulations apply and a stability assessment is required.
If your tug is 5 gross tonnage or less a stability assessment is not required and you may enter ‘N/A’ in response to this question, however the vessel must still have adequate stability per subsection 601(2) the Small Vessel Regulations.
If your tug is solely used for salvaging logs, you can select ‘N/A’ for this question.
Other guidance:
- Tug Stability: Regulation, Hazards and Loss Prevention
- TC Vessel Stability Webpage: https://tc.canada.ca/en/marine-transportation/vessel-design-construction-maintenance/vessel-stability
(Small Vessel Regulations, Section 601(2)), (Hull Construction Regulations, Part VIII Section 104-108)
Question 22 (Does the stability assessment takes into account the load due to the towing operation?)
Tugs are subject to large external forces from the towline connections to their tows. There are standards that exist to assess the impact of external forces when towing (see other guidance below). Owners are therefore strongly advised to apply the requirements for towline stability as defined by Classification Societies or other regulatory agencies. Consult a marine professional, if not certain.
Answer ‘Yes’ to this question only if the tug has a stability assessment and Question 21 was answered ‘Yes’, and the stability assessment contains an analysis of the vessel’s stability under loading due to towing. Answer “No” if not.
Answer ‘N/A’ if the tug is 5 gross tonnage or less and Question 21 was also ‘N/A’.
Other guidance:
- TP11960 “Appendix “A” - Guidance for Tug and Barge Towing Systems”
- “Ship owners’ Club: Tug and Tow – A Practical Safety and Operational Guide”
(Small Vessel Regulations, Section 601(2)), (TP 15180, Section 3.2.2)
Question 23 (If the vessel had any structural or mechanical changes since it was built, has the vessel had its stability re-assessed?)
If the vessel has been modified in any way that is sufficient to adversely affect its stability, has its stability been reassessed after the modification? See Question 21 for stability assessment requirements.
To ensure that your certificate remains valid, any change(s) to the information shown on the Certificate, including a change of address, must be reported in writing to the Small vessel Register within 30 days of the change: vr-ib@tc.gc.ca
(Hull Construction Regulations, Part VIII Section 104-108), (Small Vessel Regulations, Section 601(2))
Question 24 (Are all access and openings provided with adequate means of closing?)
This includes all external and internal doors and hatches that give access to a space below the main deck.
Sections 110 and 111 of the Hull Construction Regulations apply to openings in any watertight bulkheads fitted in the vessel.
Sections 117 to 120 of Part VIII of the Hull Construction Regulations apply for all closing appliances of any crew access openings that are fitted.
If the tug’s gross tonnage is five or less, or it is used only for salvaging logs, or it is not equipped with access openings you may enter ‘N/A’ for this question.
(Hull Construction Regulations, Part VIII Section 110-120)
Question 25 (Are door-sills and coaming fitted to prevent down flooding?)
Minimum height requirements for door sills and coamings vary depending on the deck and location of the door or access opening, the function of the space given access and other possible factors such as: if flooding of the spaces below the main deck could occur through the access opening or whether or not the vessel is equipped with crew accommodations.
Answer ‘Yes’ if all exterior and interior access openings are equipped with sills or coamings as required.
If the tug’s gross tonnage is five or less, or it is used only for salvaging logs, or it is not equipped with doors or hatches, you may enter ‘N/A’ for this question.
Sections 122 to 125 of Part VIII of the Hull Construction Regulations apply for any doors and/or hatches that are fitted to the tug.
(Hull Construction Regulations, Part VIII Section 122-125)
Question 26 (Are ventilation openings compliant with the regulations?)
Ventilation openings must be located as close to the centerline of the vessel as practicable with the lower edge of the opening not less than 915 mm above the main deck.
Ventilation openings not servicing the engine room with the lower edge less than 915 mm above the main deck may be acceptable if they are self-closing when submerged.
If the tug’s gross tonnage is five or less, or it is used only for salvaging logs, or it is not equipped with ventilation openings you may enter ‘N/A’ for this question.
Section 126 of Part VIII of the Hull Construction Regulations applies to all ventilation openings.
(Hull Construction Regulations, Part VIII Section 126)
Question 27 (Are windows and sidelights compliant with regulations?)
These provisions make requirements for the strength, type and placement of windows and sidelights, and for the fitting of deadlights.
The glass used must be as follows: For a window, toughened glass of an approved thickness, but in no case less than 6 mm thick; and for a sidelight, glass of an approved thickness.
If the tug’s gross tonnage is five or less, or it is used only for salvaging logs, or it is not equipped with windows and/or sidelights you may enter ‘N/A’ for this question.
Sections 127 to 128 of Part VIII of the Hull Construction Regulations apply for any windows and/or sidelights that are fitted to the tug.
(Hull Construction Regulations, Part VIII Section 127-128)
Question 28 (Are main deck freeing ports kept clear in order to efficiently clear water off the main deck?)
Section 521(e) of Small Vessel Regulations requires the vessel be capable of draining any accumulated water rapidly overboard. This would most likely be via freeing port openings in the bulwarks but may also be via scuppers in the drain. If all such drains are clear and free, answer ‘Yes’ to this question.
Section 139 of Part VIII of the Hull Construction Regulations makes specific requirements for the area and distribution of freeing ports and the fitting of bars or shutters, if necessary.
If the tug is not considered a decked vessel, you may enter ‘N/A’ for this question. Even if ‘N/A’, effectively being able to clear water from the tug should always be considered for safety.
(Small Vessel Regulations, Section 521), (Hull Construction Regulations, Part VIII Section 139)
Question 29 (If no deck exist, is there adequate buoyancy to remain afloat if swamped?)
This question applies to small open workboats that are used for towing operations. Buoyancy and flotation apply to small vessels of open construction that may be affected by swamping. Every such vessel must have positive buoyancy when swamped, or a gunwale of adequate height to resist swamping as a result of an emergency with the tow.
If your tug is enclosed with a deck, you can enter “N/A” for this question. Even if ‘N/A’, effectively being able to clear water from the tug should always be considered for safety.
Section 521(f) of Small Vessel Regulations applies to tugs that are undecked.
Other guidance:
- TC Vessel Stability Webpage: https://tc.canada.ca/en/marine-transportation/vessel-design-construction-maintenance/vessel-stability
(Small Vessel Regulations, Section 521)
Question 30 (Is there non-skid surfaces and storms rails in the required locations?)
Section 140 of the Hull Construction Regulations requires every working area in a ship and any exterior part of a ship on which a person may stand during the normal operation of the ship to have a durable non-skid surface. Answer ‘Yes’ to this question if the surfaces of all such areas durable are non-skid. The surface itself may be composed of a material with a texture that is inherently non-skid or covered/coated with a non-skid material.
Section 141 of the Hull Construction Regulations requires every structure on the main deck a person must walk around while the vessel normally operates to have storm-rails attached to its exterior. Each one must be attached to the structure at the ends of the rail by fastenings attached to the inside or ends of the rail; and at intermediate points not more than 1.2 m apart by fastenings attached to the bottom of the rail.
If the tug’s gross tonnage is five or less, or it is used only for salvaging logs you may enter ‘N/A’ for this question.
(Hull Construction Regulations, Part VIII Section 140 & 141)
Section 3: Navigational safety and equipment
Question 31 (Is there a DSC capable VHF radio fitted on board and is it linked to GPS?)
Every vessel that is engaged in a towing operation must be equipped with one non-portable VHF radiotelephone if the ship is operating within the VHF coverage of a Canadian Coast Guard Station. The VHF radio installation must be capable of receiving and transmitting voice communications and communications using Digital Selective Calling (DSC). In order for DSC to be effective, the vessel must also be fitted with a receiver for a global navigation satellite system. The receiver may be integral to the VHF radio installation capable of DSC. For more information, refer to the Navigation Safety Regulations 2020.
VHF/DSC equipment must be programmed with the correct Maritime Mobile Service Identity (MMSI) numbers. MMSI number must be displayed near the VHF radio. For more information on how to get a Maritime Mobile Service Identity number contact Industry Canada at 877-604-7943 or 705-941-2001 or by email at ic.spectrumcertificates-certifcatsduspectre.ic@canada.ca .
Radio installations should have a reserve battery with a capacity sufficient for the duration of the voyage. The reserve source of energy should be independent of the vessel’s engine and electrical system.
Tugs require a fitted VHF radio that is capable of Digital Selective Calling (DSC) if they are operating more than 5nm from shore in Sea Area A1. If you do not operate more than 5nm from shore, and are not in Sea Area A1, you can check mark ‘N/A’.
Other guidance:
- Maritime Mobile Service Identities (MMSIs) and Maritime Identities (MIs) : https://www.ic.gc.ca/eic/site/smt-gst.nsf/eng/h_sf06198.html
- Selling your boat or just purchase? Update your contact information
- Radio Aids to Marine Navigation at: https://www.ccg-gcc.gc.ca/publications/mcts-sctm/ramn-arnm/part4-eng.html
(Navigational Safety Regulations 2020, Section 204(1))
Question 32 (Is there a valid radio inspection certificate on board?)
Self-explanatory answer, ‘Yes’ or ‘No’.
A valid radio inspection certificate is required if the vessel is compulsory fitted with Radio communication equipment (such as a VHF DSC or an EPIRB) under the Navigation Safety Regulations, 2020.
Note: Normally Canadian Coast Guard radio inspectors conduct the inspection and issue radio certificate on behalf of Transport Canada under Ship Radio Inspection (SRI) Program. For more information on radio inspection certificate please visit Ship Radio Inspection.
Tugs that are required to have radios are also required to have a radio inspection certificate. If in question 31 you put ‘N/A’, then you can put ‘N/A’ for this question as well.
To request a radio inspection in Quebec go to:
https://www.marinfo.gc.ca/e-nav/docs/sri-dispatch-tool-en.php
For all other areas in Canada go to section 4.3.11.1 of the Radio Aids to Marine Navigation at https://www.ccg-gcc.gc.ca/publications/mcts-sctm/ramn-arnm/part4-eng.html.
Question 33 (If the tug is greater than 12m in length, is there a float free EPIRB and release unit on board? Or if the vessel is 12m or less, is there an EPIRB or PLB on board? Is the battery and release unit within their dates of validity?)
An EPIRB is an Emergency Position Indicating Radio beacon. If your vessel sinks the EBIRB will float to the surface and send a message to Search and Rescue services. In order for this to work you need to register your EBIRB so that Search and Rescue knows who they are searching for. You also need to install your EBIRB on the outside of your vessel where it can easily float upward when the vessel sinks. Check to see the expiry date on the EPIRBs batteries, and consult with the manufacturer on how to change the batteries when required.
- A vessel must be fitted with a float-free EPIRB unite if
- the vessel is engaged on a near coastal voyage, Class 1 or an unlimited voyage; or
- the vessel is more than 12 m in length and is engaged on an inland voyage or a near coastal voyage, Class 2.
- A vessel that is 12 m or less in length and engaged on an inland voyage in the waters of the Great Lakes, their connecting and tributary waters or the waters of the St. Lawrence River, or on a near coastal voyage, Class 2, must be equipped with
- a float-free EPIRB;
- a manually activated EPIRB;
- a PLB; or
- in the case of a vessel that is less than 8 m in length and that operates exclusively in sea area A1, a waterproof portable VHF handheld radio capable of DSC
The battery of the EPIRB and release unit clearly marked with their dates of validity (NSR 2020, section 209, subsection 1& 3). The validity of the EPIRB battery and float free release unit is given in the table below:
Safety Equipment |
Validity |
---|---|
EPIRB battery |
As indicated on battery |
EPRIB Hydrostatic Release Unit |
As indicated on unit |
Note: If you carry on board an EPIRB (Emergency Position Indicating Radio Beacon), ensure that it is registered properly, as it facilitates the task of the SAR authorities in an emergency and helps to eliminate false alarms. Note certain if you are up to date? Check via the National Maritime Information Database (search by vessel or station name, vessel owner name, vessel tonnage or emergency contact information).
Personal Locator Beacons (PLBs): PLBs are portable units that operate much the same as EPIRBs or ELTs. This allows rescue forces to home in on the distress beacon once the 406 MHz satellite system has provided the necessary position information. Some PLBs also allow GPS units to be integrated into the distress signal.
Not certain on which one does what? Go see https://en.wikipedia.org/wiki/Emergency_position-indicating_radiobeacon for great information on EPIRB and PLB’s.
If your vessel is not required to have an EPIRB or a PLB, then you can put ‘N/A’ as an answer to this question.
(Navigational Safety Regulations 2020, Section 209)
Question 34 (Are the required navigation lights appropriate for the vessels towing operations?)
See also guidance to question 40 for the general navigation light requirements.
Required Lights and Shapes for a vessel less than 50m in length engaged in towing:
Vessel operation |
Lights and shapes to be exhibited |
---|---|
|
Instead of the light prescribed in Rule 23(a)(i) or(a)(ii) of the Collision Regulations,
|
|
|
|
Instead of the light prescribed in Rule 23(a)(i) or(a)(ii) of the Collision Regulations,
In the waters of the Great Lakes Basin, a power-driven vessel, when pushing ahead or towing alongside, shall exhibit |
|
|
|
A special flashing light shall exhibit at the forward end of a vessel or vessels being pushed ahead, in addition to the lights prescribed above, in paragraph (f). |
|
|
|
all possible measures shall be taken to light the vessel or object towed or at least to indicate the presence of such vessel or object. |
|
|
|
|
The towing vessel must carry the navigation lights and shapes required for it to comply with the:
(Collision Regulations Rule 21 & 24)
Question 35 (Is a proper alternate system of navigation lights installed if the tugs "overall length" is greater than 15m?)
If your vessel is less than 15m in length, then put ‘N/A’ for this question.
Alternate system of navigation lights:
- For the purpose of this Rule, “alternate system of navigation lights” means a backup system that includes masthead lights, sidelights, a stern light and the lights prescribed in Rule 30 for vessels at anchor.
- This Rule does not apply to:
- vessels that are less than 15 meters in length,
- cable ferries, or
- pleasure craft.
- A Canadian vessel required by Part C to exhibit lights shall be fitted with an alternate system of navigation lights.
- In the case of vessels built before January 1, 1991, that have a gross tonnage of less than 500, the alternate system of navigation lights may consist of oil or electronic lanterns.
- If it is impracticable for a vessel or object being towed or pushed to comply with paragraph (c), spare lights shall be readily available so that the vessel or object maintains compliance with Part C.
- The alternate system of navigation lights shall be supplied by the main source of electric power and the emergency source of electric power that are referred to in section 15 of Annex I, unless otherwise provided by paragraph (g).
- In the case of vessels built before January 1, 1991, having a gross tonnage of less than 500, the alternate system of navigation lights shall be supplied by:
- the vessel’s emergency source of electric power, or
- in the case of oil or electronic lanterns, power of a capacity sufficient for the duration of the intended voyage.
- Lights using a flame shall not be used as the alternate system of navigation lights on any vessel carrying, towing or pushing cargo that is volatile or explosive.
(Collision Regulations Rule 46)
Question 36 (Are there two securely mounted searchlights on board?)
Vessels that are designed and constructed to engage in towing operations, of more than 5 gross tonnage must be fitted with 2 searchlights, except vessels that engage in towing operations only to salvage logs.
(Navigational Safety Regulations 2020, Section 121(1))
Question 37 (Is there a proper number of radar(s) or other means that can assist in navigation and in collision avoidance?)
A Canadian vessel that is a towboat must be fitted with:
- if it is of 5 gross tonnage or more and is engaged on an inland voyage or a near coastal voyage, Class 2, a radar to determine and display the range and bearing of radar transponders and of other surface craft, obstructions, buoys, shorelines and navigational marks;
- if it is engaged on a near coastal voyage, Class 1,
- echo-sounding equipment to measure and display the available depth of water, and
- two radars that meet the requirements set out in paragraph (a) and that are functionally independent of each other; and
- (c) if it is engaged on an unlimited voyage, the equipment set out in paragraph (b) and a gyro-compass to determine and display its heading by shipborne non-magnetic means.
Other Guidance
- Tug and Barge Navigational Safety: Navigation Best Practice, Safe Watchkeeping and COLREGS Compliance
- Rules of the Road (TP 14352) (PDF, 283 KB) in PDF;
- Chapter 9 of the Small Commercial Vessel Safety Guide (TP 14070E)
(Navigational Safety Regulations 2020, Section 125)
Question 38 (Before embarking has everything been taken into consideration to plan the voyage? (ie. Routes, weather, sea room, hazards, etc))
Planning a voyage:
144 (1) The master of a vessel must, before the vessel embarks on a voyage, plan the voyage taking into account the Annex to IMO resolution A.893(21), Guidelines for Voyage Planning (PDF, 486 KB), and if charts, documents and publications are required to be kept on board under NSR 2020 section 142, by using those charts, documents and publications to the extent that they relate to voyage planning.
Identifying a route,
(2) When planning the voyage, the master must identify a route taking the following factors into account:
- any relevant routing systems;
- sufficient sea room for the safe passage of the vessel throughout the intended voyage;
- all known navigational hazards (see NAVWARNs) and adverse weather conditions (Visit Marine Forecasts and Warnings for Canada)
- any marine environmental protection measures that apply; and
- actions and activities that could cause damage to the environment and measures to be taken to avoid those actions and activities.
Voyage display and position monitoring,
(3) The master of a vessel must display the vessel’s route for the voyage using a chart referred to in paragraph 142(1)(a) of NSR 2020 and plot and monitor the vessel’s position throughout the voyage on that chart.
Other Guidance:
- Take it with you: you can order free, waterproof quick reference cards that explain lateral buoys, standard day beacons, cardinal buoys and special buoys from the Transport Canada website. Contact us for Lateral Buoys and Standard Day beacons (TP 14541) and Cardinal Buoys and Special Buoys (TP 14542);
- Navigation and marine conditions website for info on nautical charts, boys, tides and currents: https://www.dfo-mpo.gc.ca/otw-am/navigation-conditions/index-eng.htm
- Working Safety on the Fraser River, Best practices for all vessels is another great product from WorkSafe BC
(Navigational Safety Regulations 2020, Section 144)
Question 39 (Are the required compass(es), charts and nautical publications on board?)
If your vessel is over 8 metres it must be fitted with a compass. This compass should be able to be adjusted and corrected for deviation as well as being capable of being lit for night viewing.
If your vessel is not more than 8 metres in length and you navigate within sight of seamarks, you are not required to carry a magnetic compass. However, due diligence and common sense should dictate that even if you are operating in areas within sight of seamarks, given the possibility of restricted visibility, this item should be considered as essential.
106(1) Every vessel, except the following vessels, must be fitted with a standard magnetic compass, independent of any power supply, that can be used to determine the vessel’s heading and to display the reading at the main steering position:
- vessels that are 8 m or less in length and navigate within sight of navigation marks; and
- cable ferries.
This compass should be one you are able to adjust and correct for deviation, as well light up for night viewing.
Standard magnetic compass
142(1) The master and authorized representative of a vessel must ensure that the most recent versions of the following charts, documents and publications, in respect of each area where the vessel is scheduled to be navigated, are kept on board:
- the reference catalogue and the applicable charts referred to in the catalogue in their largest scale, that are published by or under the authority of
- in the case of a Canadian vessel in Canadian waters, the Canadian Hydrographic Service, and
- in any other case, the Canadian Hydrographic Service or the hydrographic office or other relevant government institution of a foreign state;
- the annual edition of Notices to Mariners;
Every ship that is required to carry charts and nautical publications must be equipped with navigating accessories such as parallel rulers, dividers and binoculars.
A ship of less than 100 tons is not required to have on board these charts, documents and publications if the person in charge of navigation has sufficient knowledge of the following information, such that safe and efficient navigation in the area where the ship is to be navigated is not compromised:
- The location and character of charted
- shipping routes, Lights, buoys and marks, Navigational hazards; and
- the prevailing navigations conditions, taking into account such factors as tides, currents, ice and weather patterns.
If regulations do not require you to carry these charts, documents and publications on your ship, you should consider carrying them as a safety best practice.
Other Guidance:
- Compass correction: https://www.youtube.com/watch?v=i945NfNVuHk
- Find a nautical charts of publications dealer: https://www.charts.gc.ca/charts-cartes/dealer-depositaire-eng.html
(Navigational Safety Regulations 2020, Section 106 & Section 142)
Question 40 (Are the masthead, stern, side and/or all round white lights properly located and visible for the correct range?)
Visibility of Lights:
- In vessels of 12 m or more in length but less than 50 m in length:
- a masthead light, five miles; except that where the length of the vessel is less than 20m, three miles,
- a sidelight, two miles,
- a stern light, two miles,
- a towing light, two miles,
- a white, red, green or yellow all-round light, two miles.
- In vessels of less than 12 m in length:
- a masthead light, two miles,
- a sidelights, one mile,
- a stern light, two miles,
- an all-round light, two miles.
- In inconspicuous, partly submerged vessels or objects being towed:
Vessel 12-20 m in length
Vessel less than 12 m in length
"Masthead light" means a white light placed over the fore and aft centerline of the vessel showing an unbroken light of 225 degrees, fixed to show the light from right ahead to 22½ degrees aft of the beam on either side of the vessel.
"Sidelights" means a green light on the starboard side and a red light on the port side, each showing an unbroken light of 112½ degrees, fixed to show the light from right ahead to 22½ degrees aft of the beam on its respective side.
"Stern light" means a white light placed as near as practicable at the stern showing an unbroken light of 135 degrees, so fixed as to show the light to 22½ degrees aft of the beam on each side of the vessel.
“Towing light” means a yellow light having the same characteristics as the “stern light”
"All-round light" means a light showing an unbroken light of 360 degrees
All shapes must be black in color.
If the vessel is less than 12 m in length the vessel may exhibit an all-round white light instead of a masthead light and stern light.
Note:
The masthead light or all-round white light on a power-driven vessel of less than 12 m in length may be offset from the fore and aft centerline of the vessel if centerline fitting is not practicable, provided that the sidelights are combined in one lantern which must be carried on the fore and aft centerline of the vessel or located as nearly as practicable in the same fore and aft line as the masthead light or the all-round white light.
The full requirements are in Part C of the Collision Regulations. The navigation lights must be designed and manufactured for that purpose. Navigation lights must be properly installed, use only those bulbs recommended by the light manufacturer for the required range of visibility and ensure there is sufficient power for the lights throughout the duration of the voyage. Batteries providing power for the lights must be adequately protected and firmly secured.
Section 4: Vessel manning and crew qualifications
Question 41 (Have all crew members been trained and familiarized in towing operations?)
Before being assigned any duty on board, owner, authorized representative or master of the towing vessel must provide each member of the crew with written instructions that describe the procedures to follow to ensure their competency with:
- the shipboard equipment specific to the vessel,
- the operational instructions specific to the vessel,
- their assigned regular and emergency duties,
- the effective performance of assigned duties when performing duties vital to safety or to preventing or reducing pollution.
Note: Towing operations are often resulting in accident, and the mentoring of masters engaging in this work is very critical, and not something we have attempted to regulate, or promote well.
Additional Resource is available at:
- Transportation Safety Board's Tug Girding video)
- Ship owners Club: Tugs and Tows – A Practical Safety and Operational Guide
- Hazards and Risks of Girding During Towing Operations - SSB No.: 16/2020
Other guidance not made for the towing industry specifically but complete with best practice and free tools are available for every mariner. A very good video on how to familiarize new people on board, is available at Comité permanent sur la sécurité des bateaux de pêche du Québec (CPSBPQ) (In English as well).
(Marine Personnel Regulations Section 205(1))
Question 42 (Are copies of crew certificates of competency/training available?)
All crew members employed on the towing vessel shall carry on board their valid certificates of competency and trainings certificates and be available for inspection if required by Marine Safety Inspector.
The certificate of competency required by the master of a towing vessel not more than 15 gross tonnage is determined by the voyage made, as presented in the table below.
Minimum Required Nautical Certificates
|
Unlimited Voyage |
Near Coastal 1 |
Near Coastal 2 |
Sheltered Waters |
---|---|---|---|---|
Required Certificate |
Master Mariner |
Master 150 Gross Tonnage, Domestic |
Master Limited |
Master Limited |
Engineering Certificates
An engineer certificate is not required for towing vessel with propulsion power less than 750 kW 1000 HP.
The engineer certificate required for a towing vessel with propulsion power 750 kW or more is determined by the propulsion power of tug and type of voyage intend to make.
At least one member of the complement of the towing vessel must have a valid Marine Basic First Aid or Provincial/Territorial Recognized First Aid Training.
A towing vessel of not more than 15 gross tonnage engaged on a voyage less than 25 nautical miles from shore, every member of the complement must have a valid MED A3 or SDV-BS certificate.
A towing vessel engaged on a voyage beyond the limits of a near coastal voyage, Class 2, every member of the compliment must have a valid MED A1 or DVS certificate.
A towing vessel of not more than 15 gross tonnage engaged on a voyage less than 25 nautical miles from shore, if fitted with a VHF radio, at least one member of the compliment must have a valid ROC-M certificate obtained after January 1, 2005.
A towing vessel engaged on a voyage beyond the limits of a near coastal voyage, Class 2 or Sea Area A1, if fitted with a VHF radio, at least one member of the complement must have a valid ROC-MC certificate.
For more detailed information, please refer to the Marine Personnel Regulations or contact your local TCMSS office. See https://tc.canada.ca/en/marine-transportation-regions
(Canada Shipping Act 2001, Section 18), (Marine Personnel Regulations Section 130, 205(1) & 206(2))
Question 43 (Is there enough crew on board to handle an emergency?)
Your tug must be manned by a sufficient crew to respond to the following foreseeable emergencies on board: fire, man overboard, engine failure, flooding, grounding, pollution, distress calls and launching life rafts.
Three main factors determine the minimum number of crew members required for ordinary operating conditions: vessel size, number of passengers and area of operation. Thereby, every vessel must have a sufficient number of qualified and experienced crew members who are able to respond to foreseeable emergency situations.
The crew should be able to respond to the following emergencies on board: fire, man overboard, engine failure, flooding, passenger control, distress calls and launching life rafts. Many of these tasks are required to be done simultaneously, for example: maintaining order and calm among the passengers, sending out distress messages if required, operating the vessel’s pumping and emergency power system, and launching the life raft (if applicable).
Although the minimum safety manning document is not required on your tug, you can write to us if you have any questions via SafeManning-EffectifMinimal@tc.gc.ca
Other guidance:
Vessel Fire Safety Regulations
Life Saving Equipment Regulations
(Marine Personnel Regulations Section 207(1))
Question 44 (Are the crew trained on the emergency equipment on a regular basis?)
You must have on board written safety procedures which must be implemented. In addition, you must familiarize all persons on board with:
- the location and use of all safety equipment;
- all the measures they must take to protect persons on board, in particular measures to:
- prevent persons from falling overboard,
- retrieve persons who have fallen overboard,
- protect limbs from rotating equipment, and
- avoid ropes, docking lines, lifting gear other equipment that may pose a safety hazard to persons on board;
- in the case of towing, procedure to release tow hook in case of an emergency;
- all the firefighting measures they must take to prevent fires and explosions on the vessel;
- if the vessel has a deck or deck structure, all the measures they must take to maintain water tightness and weather tightness and to prevent flooding of the interior spaces of the hull or, if the vessel has no deck or deck structure, all the measures they must take to prevent swamping of the vessel;
- the operation of towing and lifting equipment and the measures they must take to prevent overloading of the vessel.
Transport Canada has created operational and safety procedure templates you can download and adapt for your use. Please visit the following webpage to learn more at Templates for Small Commercial Vessel Procedures and Records
Other guidance not made for the towing industry specifically but complete with best practice and free tools for every mariner are available via Gearing up for safety from WorkSafe BC. Free Safety Checklists can be downloaded and you can make them specific with your vessel’s safety equipment.
(Canada Shipping Act 2001, Section 106), (Marine Personnel Regulations Section 206)
Question 45 (Is there a record of training kept for each crew member?)
As the owner or Master of the towing vessel you are required to maintain a record of those training (see question 44 above). The record must be readily available, and a copy must be kept on board your vessel. If your vessel does not travel more than five nautical miles from its home port, you may choose to keep it at your home port.
The record must contain:
- the name of each member of the complement who has been trained,
- the equipment they were trained on,
- the subject-matter they were trained on, and
- the days on which they were trained.
Transport Canada has created operational and safety procedure templates you can download and adapt for your use. Please visit the following webpage to learn more at Templates for Small Commercial Vessel Procedures and Records.
(Marine Personnel Regulations Section 205 & 206(2))
Question 46 (Are crew members able to use safety, firefighting and operational equipment effectively?)
The owner and the operator of a towing vessel shall ensure that;
- procedures are established for the use of the towing vessel’s life-saving appliances and fire extinguishing equipment in case of an emergency; and
- the crew practices the procedures so as to be at all times proficient in carrying them out. Before being assigned any duty on board, each member of the crew shall be provided with written instructions that describe the procedures to be followed in order to ensure their competency with:
- The shipboard equipment specific to the vessel;
- The operational instructions specific to the vessel;
- Their assigned regular and emergency duties; and
- The effective performance of assigned duties vital to safety or to the prevention or mitigation of pollution.
(Marine Personnel Regulations Section 205(1))
Question 47 (Are there enough certified crew to maintain a deck watch for the entire voyage?)
Your tug must be manned by a sufficient number of crew so to ensure safe deck watch can be maintained during the entire voyage without jeopardizing the hours of rest required by the master and crew. Master or the owner will ensure that the crew holds a certificate appropriate to the class of vessel and the area in which the vessel operates and the duties to be performed by the person.
(Marine Personnel Regulations Section 207(1))
Question 48 (Are crew members getting at least six hours rest in a 24-hour period or at least 16 hours rest in a 48-hour period? Is it documented?)
Master of a towing vessel which is engaged on sheltered waters voyage, NC 2 or NC1 voyage and does not operate in the waters of foreign country. Must ensure that all crew including him/herself have:
- at least six consecutive hours of rest in every 24-hour period,
- at least 16 hours of rest in every 48-hour period; and
- not more than 18 hours but not less than six hours elapse between the end of a rest period and the beginning of the next rest period.
Master of a towing vessel engaged on NC 2 or NC1 voyage while the vessel is in the waters of a foreign country or unlimited voyage, must ensure that all crew members including him-/ herself:
- not work more than 14 hours in any 24-hour period or more than 72 hours in any 7-day period; or
- have at least 10 hours of rest in every 24-hour period and 77 hours of rest in every 7-day period.
The master shall also ensure that:
- the hours of rest are divided into no more than two periods, one of which is at least 6 hours in length; and
- the interval between two consecutive rest periods does not exceed 14 hours.
The master of a vessel shall keep a record of every crew member’s daily hours of work or hours of rest until the crew member is discharged. This record will be verified by the Marine Safety Inspector during monitoring inspection.
In addition, the master has to ensure that all documentation for rest hours is done appropriately.
Depending on the watch composition, some watch systems are 6 hours on and 6 hours off, 12 hours on and 12 hours off, 4 hours on and 8 hours off. It all depends on the number of certificated persons on board. Also depending on the nature of the tow would dictate how many watch officers could be onboard.
Other guidance:
TSB Backgrounder – Fatigue in the transportation industry (PDF, 206 KB) and Fatigue management in rail, marine and air transportation
(Marine Personnel Regulations 320)
Question 49 (If operating with a master, limited certificate, does the certificate include the vessel being operated and the area of operation?)
Master Limited would have restrictions/limitations for vessel and specific zone of operation, thus, the certificate of competency can only be used on-board the listed vessel(s) and area of operation. These certificates are limited.
(Marine Personnel Regulations 212)
Section 5: Pollution prevention
Question 50 & 51 (are measures in place to prevent discharge sewage over board?) (are measures in place to prevent discharge of other liquids that are prohibited to be discharged overboard?)
In order to avoid any unwanted discharge, a holding tank’s construction should,
- not compromise the integrity of the hull;
- be of structurally sound material that prevents the tank contents from leaking;
- prevent the potable water system or other systems from becoming contaminated;
- be resistant to corrosion by sewage;
- have an adequate volume for the ship’s human-rated capacity for maximum intended voyage duration;
- include a discharge connection and piping system for the removal of the tank contents at a sewage reception facility;
- be designed so you can determine the level of sewage in the tank without opening the tank and without contacting or removing any of the tank contents; or be equipped with a device that allows the determination to be made; and
- include a ventilation device whose outlet is on the exterior of the ship, in a safe location away from ignition and areas usually occupied by people; and has a flame screen of non-corrosive material fitted to the vent outlet.
Note: A toilet fitted on a tug must be secured in a manner that ensures its safe operation in any environmental conditions liable to be encountered.
Example of Acceptable Facility:
(Vessel Pollution and Dangerous Chemicals Regulations 95), (Small Vessel Regulations 1002)
Section 6: Electrical systems/batteries
Question 52 (Does the electrical system conform to the designated standards?)
Electrical system must be made in accordance with Ship Electrical Standards (2018) –TP 127.
In the case of an electrical system of 50 volts or more, the vessel has to meet:
- the requirements of TP 127 S1.6.1 Emergency Electrical Power in Ships of Group 5 and Part I General Requirements for Ships of Groups 1 to 5B ; or
- Where TP 127 does not set out specific requirements in respect of the design, construction, installation or inspection of electrical equipment, these codes, rules and standards should be consulted for guidance as to the appropriate safety standards that are accepted by the marine industry:
- the most recent rules of IEEE Std 45 Recommended Practice for Electrical Installations on Shipboard;
- the most recent rules of the IEC Publication 60092 “Electrical Installations in Ships”;
- the most recent rules of a recognized Classification Society; or
- the most recent rules or codes issued by Societies or Administrations, other than recognized Classification Societies.
In the case of an electrical system of less than 50 volts, it the vessel has to meet:
- the requirements of TP 127 Part II Electrical Systems Less than 50 Volts; or
- the requirements of American Boat and Yacht Council Standards E-10, Storage Batteries, and E-11, AC and DC Electrical Systems on Boats.
(Ship Electrical Standards (2018) –TP 127E), (Small Vessel Regulations 608)
Question 53 (Are all cables in the electrical system suitable for marine use?)
Conductors and flexible cords for lighting, power, propulsion and communication circuits in marine installations shall be/have:
- constructed and tested by a certifying authority;
- of a suitable commercial grade with stranded copper conductors and rated for at least 75°C service;
- a protective covering of either watertight metallic sheath or impervious non-metallic sheath, compatible with the insulation; and
- suitable for operation at the temperature of the equipment.
In the case of an electrical system of 50 volts or more, the requirements of TP 127 Part I Section 12 Construction of Cables shall be followed or those of an equivalent standard. In the case of an electrical system of less than 50 volts, it shall meet TP 127 Part II Section 56 Cables or equivalent standards.
(Ship Electrical Standards (2018) –TP 127E), (Small Vessel Regulations)
Question 54 (Are all joints and connections mechanically and electrically secure and made only in junction or outlet boxes?)
Installation of cables shall be:
- effectively supported and secured in order to prevent chafing or other injury; and
- routed as high as possible above the bilge with prime consideration given to the protection of the wiring from mechanical damage and heat damage.
Joints and connections in all electrical conductors shall be:
- mechanically and electrically secure and made only in junction or outlet boxes; and
- capable of withstanding the vibration and movement encountered in normal service.
In the case of an electrical system of 50 volts or more, the vessel shall meet the requirements of TP 127 Part I Section 13 Installation of Cables or equivalent standards. In the case of an electrical system of less than 50 volts, it shall meet TP 127 Part II Section 58 Distribution or equivalent standards.
(Ship Electrical Standards (2018) –TP 127E), (Small Vessel Regulations)
Question 55 (Are the batteries properly secured, protected from mechanical damage and properly vented?)
Installation of batteries:
- Batteries shall be located where they are not exposed to excessive heat, extreme cold, spray, steam or other conditions which would impair performance or accelerate deterioration;
- Batteries shall not be installed in sleeping quarters; and
- All rooms, lockers and boxes for storage batteries shall be arranged, and ventilated to avoid accumulation of flammable gas.
In the case of an electrical system of 50 volts or more, the vessel shall meet the requirements of TP 127 Part I Section 19.4 Installation and Location or equivalent standards. In the case of an electrical system of less than 50 volts, it shall meet TP 127 Part II Section 55 Batteries or equivalent standards.
(Ship Electrical Standards (2018) –TP 127E), (Small Vessel Regulations)
Section 7: Fuel systems
Question 56 (Are the fuel system designs complaint with the regulations?)
Self-explanatory answer: ‘Yes’ or ‘No’.
Note: no person shall install or maintain a fuel tank or a fuel system on a vessel in a manner that permits or is likely to permit leakage or spillage of fuel into the hull or into the environment. Fuel tanks must be provided with protection from leakage caused by shock, corrosion, abrasion or fire.
Note: spilled fuel must not enter the vessel:
- prevent fuel spillage, protect fuel lines from damage, prevent leakage in the fuel system by using appropriate couplings and connectors;
- keep save-alls clean;
- clean up any spilled fuel immediately; and
- do not allow spilled fueled to accumulate in the bilge or any enclosed space.
(Marine Machinery Regulations, SCHEDULE XII, Part 1 (Items 1-26)), (Small Vessel Regulations)
Question 57 (Are fuel tank closing arrangements tested on a regular basis and capable of being closed from outside the space in which they are located?)
Are the valves on the fuel oil tanks in compact spaces capable of being closed from outside the space in which they are located (using extended spindle valves, quick closing valves or wire for example)?
Note: Fuel oil tanks in compact spaces capable of being closed from outside the space in which they are located (using extended spindle valves, quick closing valves or wire).
(Marine Machinery Regulations, SCHEDULE XII, Part 1 Items 16-17)
Question 58 (Are measures in place to manage the fuel tank quantities during the voyage?)
Self-explanatory answer: ‘Yes’ or ‘No’.
(Marine Machinery Regulations, SCHEDULE XII – Part 1 (Item 13))
Question 59 (Can oil supply to appliance burners for cooking and cabin hot-air heating be shut off from outside of the spaces in which they are located?)
For appliances that burn liquefied petroleum gas items 3 & 4 of Schedule XIII, division II require fuel cylinders be stored outside any accommodation or other spaces where cooking or heating appliance are located.
(Marine Machinery Regulations, SCHEDULE XII, Part 1 (Item 12)), (Marine Machinery Regulations, SCHEDULE XIII, Division II (Item 3-4))
Section 8: Machinery
Question 60 (Are all machinery constructed and installed in accordance with applicable rules or codes?)
Self-explanatory answer: ‘Yes’ or ‘No’.
(Marine Machinery Regulations, Section 4-5)
Question 61 (Are the steering systems installation compliant with the regulations?)
All components of the steering systems gear must be protected from obstructions, excessive heat and mechanical wear. Main steering gears shall be controllable from the bridge and from an alternative location in the steering gear compartment or other suitable location taking into account operational and risk factors.
(Marine Machinery Regulations, Schedule VII – Division 1 – (Items 1-23) & Division III – (Items 1-9)))
(Hull Construction Regulations Section 89-90 & 130)
Question 62 (Are the bilge and ballast pumping systems compliant with the regulations?)
Every vessel that carries ballast water other than permanent ballast must complies with the requirements of the Ballast Water Regulations.
Every Tug shall be fitted with a bilge pumping system that complies with the regulation and fitted with or accompanied by sufficient piping or hose to enable water to be pumped from the bilge space of the vessel over the side of the vessel.
In addition bilge system shall complies with following standards:
- A bilge pumping system shall be provided with a mechanical pump;
- The pump shall be self-priming and be designed to run dry without damage;
- Engine driven pumps are acceptable only if they can be run independently from the propulsion shafting;
- The piping arrangement shall ensure that no back siphoning can occur and marine type strainers shall be provided on the suction line from each compartment;
- The piping shall be of metal, rigid plastic, non-collapsible and non-oil degradable hose with flanged, screwed, or robust double-clamped connections, where practicable;
- The piping shall be not less than 25 millimetres (1 inch) in diameter, except that for small compartments piping 18 millimetres (3/4 inch) in diameter may be acceptable if the pump-out time is under five (5) minutes;
- The automatic bilge pump or a bilge pumping system has a minimum capacity of 0.91 Litres/second (14½ US Gallons/minute);
- When an automatic bilge pump is fitted, a visual signal shall be provided at the operating position to indicate when the pump is running and a manual overriding switch shall be provided at the operating position.
(Ballast Water Regulations (SOR/2021-120), (Small Vessel Regulations Section 609), (Marine Machinery Regulations SCHEDULE XV)
Question 63, 64, & 65 (are measures in place to periodically verify bilge water level?), (are crew provided with clear instructions on how to lower the tug's bilges?) & (are crew familiarized with the propulsion machinery shutdown procedures in case of engine faults while towing?)
Self- explanatory answer: ‘Yes’ or ‘No’.
Note: Authorized representative has to insure that,
- all machinery and equipment are in satisfactory operational condition;
- Bilge should be fitted with high level alar and alarm should be tested regularly to ensure they are operative
- safety procedures are made and implemented for safe operation of the vessel and that the crew are well trained.
Question 66 (Are effective guards provided for protection against machinery that moves, is hot or is otherwise hazardous?)
Self-explanatory answer: ‘Yes’ or ‘No’.
Note: Machine guarding are provided to protect the crew in the machine area from hazards such as those created by point of operation, ingoing nip points, rotating parts, flying chips and sparks. Examples of guarding methods are-barrier guards, two-hand tripping devices, electronic safety devices, etc.
(MMR, Schedule XVI Section 4, Item 10)
Section 9: Life saving and fire safety equipment
Question 67 (Is there a marine first aid kit on board?)
A first aid kit shall be packed in a waterproof case capable of being tightly closed after use and shall be either:
- A first aid kit that meets the requirements of the Maritime Occupational Health and Safety Regulations or of provincial regulations governing workers‘ compensation (with the addition of a resuscitation face shield and two pairs of examination gloves if the kit does not already contain them); or
- A marine emergency first aid kit that contains the following:
- An up-to-date first aid manual or up-to-date first aid instructions, in English and French
- 48 doses of analgesic medication of a non-narcotic type
- Six safety pins or one roll of adhesive first aid tape
- One pair of bandage scissors or safety scissors
- One resuscitation face shield
- Two pairs of examination gloves
- 10 applications of antiseptic preparations
- 12 applications of burn preparations
- 20 adhesive plasters in assorted sizes
- 10 sterile compression bandages in assorted sizes
- 4 meters of elastic bandage
- Two sterile gauze compresses
- Two triangular bandages
- A waterproof list of the contents, in English and French.
Other Guidance:
- Transport Canada – Marine Transportation – First Aid Kit
- Maritime Occupational Health and Safety Regulations
(Small Vessel Regulations 504)
Question 68 (Do you carry a lifejacket of an appropriate size or an appropriate PFD for each person on board?)
Lifejackets
Lifejackets come in red, orange or yellow. This makes you much easier to see in the water. Right now there are three Canadian-approved lifejacket types to choose from, with new ones from UL coming soon.
- Safety of Life at Sea (SOLAS) lifejackets meet very high performance standards and are approved for all vessels. They,
- will turn you on your back in seconds to keep your face out of the water, even if you are unconscious;
- come in two sizes: for those over 32 kg (70 lbs) and those less than 32 kg; and
- are available in comfortable and compact inflatable configurations that can be automatically, manually or orally inflated.
- Standard Type lifejackets are approved for all vessels, except SOLAS vessels. They:
- Will turn you on your back to keep your face out of the water, even if you are unconscious; and
- Come in two sizes: for those less than 40 kg (88 lbs) and those greater than 40 kg.
- Small Vessel lifejackets are approved for small vessels. They:
- Have less flotation than Standard Type lifejackets;
- Will turn you on your back, but may do so more slowly;
- Come in two models: keyhole and vest; and
- Come in three sizes.
Personal Flotation Devices (PFDs)
Transport Canada will accept a PFD as the sole flotation device on a vessel operating within Near Coastal Voyages, Class 2, if it meets the following conditions. Please refer to Ship Safety Bulletin: Wearing and using flotation devices small non-pleasure craft - SSB No.: 06/2012
The PFD must:
- be worn at all times in an open vessel and when on deck on a vessel of closed construction, and underway as required by the Small Vessel Regulations;
- be approved by Transport Canada, or Canadian Coast Guard;
- provide a minimum 100 newton buoyancy unless it is an approved suit or jacket designed to offer thermal protection as well as buoyancy;
- be of a highly visible colour (yellow, orange, or red); for inflatable PFDs, it is the internal bladder (the part that pops out when activated) that must be a highly visible colour, not the external cover;
- be fitted with retro-reflective tape and a whistle, and
- be self-righting, unless it is an approved suit or jacket designed to offer thermal protection as well as buoyancy.
Note that Transport Canada is currently reviewing new Lifejackets standards. If you are not certain if your Lifejacket is good for commercial usage, contact your local TCMSS office. See https://tc.canada.ca/en/marine-transportation-regions.
Other Guidance:
- Inspection and Maintenance of Inflatable Lifejackets and Personal Flotation Devices - SSB No.: 12/2019;
- Acceptance of Level 70 Buoyancy Aids Certified to UL12402-5 as Personal Flotation Devices;
- Acceptance of Specialized Life Preservers instead of Approved Lifejackets or Personal Floatation Devices (PFDs) for emergency response teams
- Marine Safety Management System - Tier I - Policies
(Small Vessel Regulations 506)
Question 69 (Are there two lifejackets in the wheelhouse that are easily accessible?)
Self-explanatory – answer will be ‘Yes’ or ‘No’.
The number two is the minimum at all time. Do take note that one lifejacket per person on board is the minimum requirement.
(Small Vessel Regulations 521)
Question 70 (If re-boarding height is greater than 0.5 metres is a re boarding device available?)
When the freeboard exceeds 0.5 metres (approximately 20 inches) you will need a re-boarding device. However, your vessel already meets this requirement if it has transom ladders or swim platform ladders. An outboard engine may not be used as a re-boarding device.
(Small Vessel Regulations 506)
Question 71 (If there are two or more persons on board and your vessel is more than 8.5m in length, do you carry on board one or more life rafts with total capacity sufficient to carry all the persons on board?)
If there are two or more persons on board a tug that is more than 8.5 metres in length, it shall carry on board one or more life rafts with a total capacity sufficient to carry all the persons on board. The life raft or buoyant apparatus (except for a life raft packed in a valise-type container) must be stored in a manner that allows it to automatically float free if the vessel sinks.
Other guidance:
- How to install a Hammar H20 Small Raft on YouTube;
- Hammar H20 - How it works on YouTube
- How to Install Hammar H20 Hydrostatic Easy Release Unit on YouTube
Question 72 (Is the life raft serviced at proper interval?)
A life raft must be serviced at the intervals (for example, annually or every two years) set out in Section 2 of Schedule IV in the Life Saving Equipment Regulations, it must be serviced at a service station accredited by the manufacturer of the life raft. The location and last date of service should be clearly marked on the life raft. With the exception of a life raft packed in a valise-type container, a life raft must be stored in a manner that allows it to automatically float free if the vessel sinks.
(Small Vessel Regulations 21), (Life Saving Equipment Regulations)
Question 73 (Have you ensured that all fire extinguishers in, or stored in, the accommodation space (sleeping quarters) does not contain a gas extinguishing agent?)
An accommodation space is a room that you sleep in overnight. You are required to have a fire extinguisher for your accommodation space, but it can’t contain a gas such as CO2, Halon, or FM200, as these gasses will suffocate people. The fire extinguisher in the accommodation space is required to be a water, foam, or dry chemical extinguisher.
(Small Vessel Regulations 512(4))
Question 74 (If the vessel is equipped with a fuel-burning cooking, heating or refrigerating appliance, is an additional 1a: 5b: c fire extinguisher installed on board?)
What does the 1A: 5B: C rating mean? The letters refer to the type of fire, and the numbers refer to the amount of fire the extinguisher can handle.
Fire Class |
Appropriate for fires involving: |
Number refers to: |
---|---|---|
A |
Combustible materials such as wood, cloth, paper, rubber or plastic. |
How much water the extinguisher is equal to – the standard uses a formula of 1 ¼ gallons (US) multiplied by the rating number. For example, a 1A: 5B: C extinguisher is equal to 1 ¼ gallons of water to fight a Class A fire. |
B |
Flammable or combustible liquids such as oil, gasoline or grease. |
The amount of square feet of a Class B fire that should be extinguished if the extinguisher is used correctly by an untrained person. For example, a 1A: 5B: C extinguisher should be able to extinguish 5 square feet of a Class B fire. |
C |
Electrical equipment such as appliances and wiring. |
No number – the “C” only denotes that the extinguisher is safe for a Class C fire. |
Fire extinguishers are to be maintained in good working order and serviced (tagged) by approved technicians as per the manufacturers recommended schedule and practice.
(Vessel Fire Safety Regulations – SOR/2017-14), (Small Vessel Regulations 521)
Question 75 (Are extinguishers properly serviced at required intervals?)
Check your Fire extinguishers monthly to make sure that the needle on the pressure gauge is in the green zone. If it is not in the green zone have it serviced and refilled. Have your fire extinguisher serviced yearly and purchase a new one after 6 years. Powder extinguishers should be tumbled at least once a month, to ensure that the vibrations of the tugs have not compressed the powder into a lump.
Question 76 (Are at least two means of escape from the wheelhouse directly to the outside?)
One means of escape can be the door to the wheelhouse. Your second means of escape can be another door or a window. If it is a window make sure you are able to fit out of the window in an emergency, and there is an exit point for when the vessel begins to heel prior to capsizing.
(Small Vessel Regulations 521)
Question 77 (Are there at least two escapes from each normally occupied space?)
To minimize the chance of one incident blocking both escapes, the means of escapes must:
- be as remote from each other as practicable;
- have a means of exiting to the outside; and
- have a clear opening size of at least 560 millimetres x 560 millimetres.
Only one means of escape is required if:
- the space is not normally occupied;
- the dimensions of the space do not permit more than one means of escape; or
- the deck area is not more than 28 metres.
Other Guidance:
Construction Standards for Small Vessels (2010) – TP1332E – Section 10.2 Fire Safety
(Hull Construction Regulations 115)
Question 78 (Are the heat detectors in the engine space and fire detectors in the accommodation spaces (sleeping quarters) fitted with an audible alarm of at least 84db?)
Fire detectors must be listed for marine use by a product certification body or type approved by a classification society.
On all vessels of not more than 12 metres and on workboats of not more than 15 metres not provided with overnight accommodations, detectors with an integral alarm may be installed. The alarm level shall not be less than 84 decibels.
Other Guidance:
Construction Standards for Small Vessels (2010) – TP1332E – Section 10.3 Fire Detection and Alarm
(Small Vessel Regulations 516)
Question 79 (Are 3 distress flares, type A, B or C (no smoke signals, type D) on board?)
When buying marine distress flares, you should look for a Transport Canada approval stamp or label. Remember that flares are only good for four years from the date of manufacture (not the date of purchase), which is stamped on every flare. You should also ask the manufacturer how to dispose of your expired flares. Flares should be kept within reach and stored vertically in a cool, dry location (such as a watertight container) to keep them in good working condition.
There are four types of approved flares: A, B, C and D. Type A: rocket parachute flare, Type B: multi-star flare, Type C: hand flare, Type D: smoke signal (buoyant or hand-held).
(Small Vessel Regulations 507)
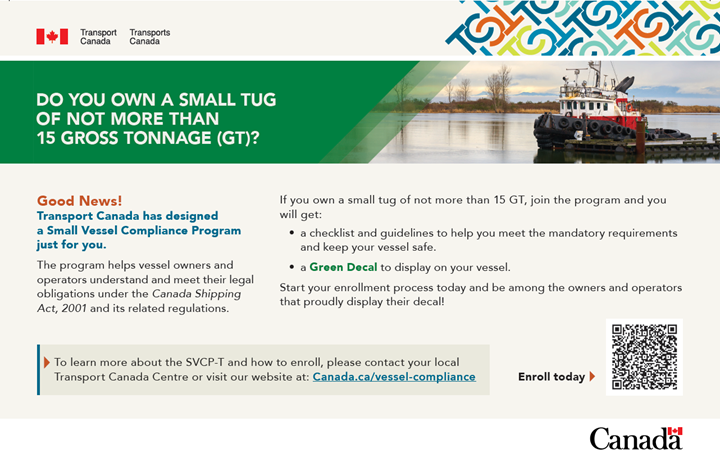